Permanent magnet rotor e1655961736623.jpeg
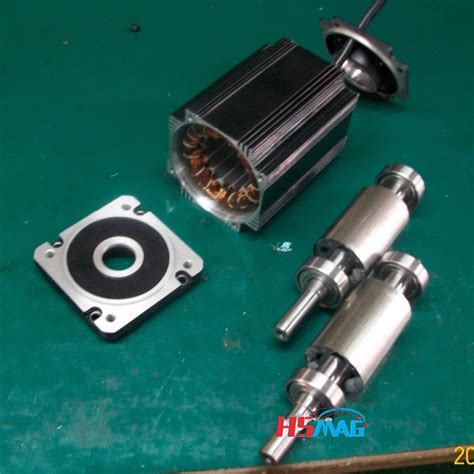
Feb 21, 2023 · An interior permanent magnet synchronous motor (IPMSM) with ‘VV—’ shape rotor topology structure is proposed. The established two-dimensional (2D) parameterized finite element analysis (FEA) models are used to analyze and compare the output average torque, torque density, air-gap flux density and back electromotive force (EMF) of the IPMSM with ‘V’ shape, ‘V—’ shape, ‘VV ... Similar to type Ⅰ, this configuration also forms a series magnetic circuit between the inner stator, outer stator and rotor. The rotor structure of type Ⅲ is similar to that of type Ⅱ, but the magnetisation direction of the inner and outer PMs located on the same axis are opposite. In this rotor structure, the rotor yoke contains ...Aiming at the rotor strength problem of high speed permanent magnet synchronous motor (HSPMSM), a design method for maximum outer diameter of permanent magnet is proposed. Firstly, on the basis of mechanics of materials, the stress analytical model of HSPMSM rotor with anisotropic material is established. Then, the …
Did you know?
2.1 Selection of Solution Variants for Analysis. In this study, an analysis of the selection of the number of stator slots to the number of magnetic poles was carried out for the structure of the Permanent Magnet Synchronous Motor (PMSM) with an external rotor, with surface mounted magnets (SPM) with a double-layer, concentrated winding …Non−Magnetic Rotor Core Rotor Magnets Rotor Pole Pieces Figure 2: Axial View of a Flux Concentrating Motor The geometry of one type of internal magnet motor is shown (crudely) in Figure 2. The permanent magnets are oriented so that their magnetizationis azimuthal. They are located between wedges of magnetic material (the pole pieces) in …Measure Skewing Angle. MagScope software makes it easier than ever to measure the skewing angle of skewed permanent magnet rotors, enabling the detection of skewing angle deviations. The right figure shows an example of the step skew on an IPM (Interior Permanent Magnet) rotor, represented in a cross-section graph with automatic zero …
This paper proposes a new design method for sleeve thickness and interference based on a multi-dimensional visualization algorithm that overcomes difficulties in solving. The contact pressure between the rotor core and the permanent magnet, the maximum equivalent Mises stress of the permanent magnet, and the maximum …Permanent-Magnet Motors Wen L. Soong, Member, IEEE, and Nesimi Ertugrul, Member, IEEE Abstract— This paper compares the field-weakening perfor-mance under rated and overload conditions of synchronous reluctance and interior permanent-magnet motors against that of a baseline 2.2-kW induction machine. Four prototype rotors basedNov 11, 2021 · According to the location of permanent magnet on the rotor, the permanent magnet synchronous motor rotor mainly has two different structures: surface-mounted and buried. Due to the strength limitation of silicon steel sheets, the application of buried rotor in the high-speed field is relatively smaller than surface-mounted rotor. The fundamental operation of a permanent magnet motor is like most electric motors; the outer stator holds windings of coils fed by a power source, and the rotor freely rotates based on the forces imparted by the stator coils. Many of the same basic principles for induction motors hold true for permanent magnet motors, and more information can ...
Since the teeth of the stator and the magnetic bridge of the rotor are prone to magnetic saturation, the grids in these places are encrypted, as shown in Figure 2. The specific mesh settings are as follows: stator teeth 0.2 mm, stator yoke 2 mm, rotor edge 0.2 mm, rotor yoke 2 mm, and permanent magnet 2 mm.A magneto-structural combined dimensional and topology optimization approach for interior permanent magnet synchronous machine (IPMSM) rotor design is proposed using the solid isotropic material with penalization (SIMP) density-based topology optimization method. This method optimizes the location and dimensions of the …Axial flux permanent magnet synchronous motors (AFPMSMs) have been widely used in wind-power generation, electric vehicles, aircraft, and other renewable-energy applications owing to their high power density, operating efficiency, and integrability. To facilitate comprehensive research on AFPMSM, this article reviews the developments in … ….
Reader Q&A - also see RECOMMENDED ARTICLES & FAQs. Permanent magnet rotor e1655961736623.jpeg. Possible cause: Not clear permanent magnet rotor e1655961736623.jpeg.
This paper overviews high-speed permanent magnet (HSPM) machines, accounting for stator structures, winding configurations, rotor constructions, and parasitic effects. Firstly, single-phase and three-phase PM machines are introduced for high-speed applications. Secondly, for three-phase HSPM machines, applications, advantages, and …This paper is focused on the optimal design, simulation, and experimental testing of a counter-rotating double-rotor axial flux permanent magnet synchronous …The prototype machine is an axial-flux permanent-magnet machine with a two-rotor–one-stator configuration. The nominal power of the machine is 300 W and the nominal rotational speed is 500 rpm. The magnets are neodymium iron boron magnets. Twelve magnets are mounted on the rotor surface and 12 magnets buried on the rotor (Fig. 12a).
The permanent magnet motor tends to have larger step angles, 7.5° or 15°, than the variable reluctance motor. The hybrid motor typically has 200 rotor teeth and rotates at 1.8° step angles. They have high static and dynamic torque and can run at very high step rates. As a consequence they are very widely used. Permanent Magnet Motors - External Rotor. The W series external-rotor permanent magnet motor combines the high strength alloy material with the patented one-piece fan …Mar 20, 2021 · Reluctance is a function of rotor position in a variable reluctance motor. Sequential switching (Figure below) of the stator phases moves the rotor from one position to the next. The mangetic flux seeks the path of least reluctance, the magnetic analog of electric resistance. This is an over simplified rotor and waveforms to illustrate operation.
paiiing In order to get rid of the bulky and lossy differential gears and to enhance the system robustness, the magnetic differential (MagD) system is proposed after the mechanical differential (MechD) and electronic differential (ElecD) systems. The MagD system is mainly composed of the double-rotor (DR) stator-permanent-magnet (PM) …The traditional bearingless synchronous reluctance motor (BSynRM) with salient pole rotor has some drawbacks such as high suspension force ripple, low torque density and low power factor. To overcome the above shortcomings, the permanent-magnet-assisted bearingless synchronous reluctance motor (PMa-BSynRM) is … corpus christi cronica posttouren External rotors of “outrunner” type. Rotors with additional bandage (Polyglas, Kevlar, carbon) Rotors with protecting sleeve. Contact us. Jan Kratochvil ml. +420 607 570 823 …Aug 1, 2022 · The axial lengths of the IPM rotor and the SynRM rotor are respectively changed by changing the parameters L and H. It shows that when the width of the permanent magnet L is 85 mm and the thickness H is 4 mm, the maximum total torque reaches 174.2 N m. The length of the permanent magnet rotor is 141.17 mm. Download : Download high-res image (177KB) scp 3008 script pastebin In the same way in , through FEM simulations and experimental results, a simple dynamic abc model for brushless permanent magnet motors, under demagnetisation faults, is presented and validated. The strategies based on the analysis of the harmonics produced by rotor demagnetisation in the phase currents or the EMF are …Feb 9, 2018 · Electric machines with permanent magnet rotors are becoming increasingly popular due to the high power density that they offer relative to other configurations. Where the speed of rotation is high, the magnets are typically mounted on the surface of the rotor and retained by an outer sleeve. In the literature, a variety of analytical models have been proposed to aid the mechanical design ... seven oitpercent27s not rocket science answer key557685 Harmonic Distortion is very low at <2% giving superior waveform, meaning that our low rpm permanent magnet generators help you guarantee the safe operation of modern sensitive electronic equipment. When using our low rpm pmg generators, power density is increased using inverter technology, where the traditional excitation winding systems are ... edie The accurate calculation and reduction of electromagnetic force waves are important prerequisite for the evaluation and optimization of electromagnetic vibration. In this paper, an accurate calculation method of air gap permeance is proposed, the air gap flux density and the resulting electromagnetic force waves of 6p36s surface-mounted … bear lake getaway.en gbcompute statslaunch trampoline park prince george Feb 21, 2023 · An interior permanent magnet synchronous motor (IPMSM) with ‘VV—’ shape rotor topology structure is proposed. The established two-dimensional (2D) parameterized finite element analysis (FEA) models are used to analyze and compare the output average torque, torque density, air-gap flux density and back electromotive force (EMF) of the IPMSM with ‘V’ shape, ‘V—’ shape, ‘VV ... (PMSM) into the market. Permanent magnet synchronous machines have been applied to servo drives for a long time already, and nowadays, there are quite large permanent magnet synchronous machines also in industrial use. In wind mill generators, the development has currently been in the direction of permanent magnet machines.